Issue description
When cutting materials using S1's diode laser module, the edges of the cut appear yellowed, dark brown, or blackened (scorched), instead of clean.
S1’s diode laser is not suitable for cutting or processing the following materials. Attempting to cut them may lead to poor results or safety hazards:
1. Transparent materials (e.g., clear acrylic, glass)
2. Mirrored surfaces (e.g., mirror acrylic)
3. Materials that are primarily blue in color (as they reflect blue light)
4. Certain types of extruded acrylic.
For a list of recommended materials and settings, please refer to the official xTool material library: https://materials.xtool.com.
Possible causes
- Incorrect processing parameters (power, speed, passes, focus offset)
- Incorrect focal distance setting
- Dirty or damaged laser lens and lens protector
- Air Assist not used or configured incorrectly
- Air pump tube loose or disconnected
- Malfunction within the laser module
Troubleshooting procedure
Please follow these steps systematically to diagnose and resolve the issue.
#1 Verify processing parameters:
Incorrect settings are a common cause of scorching.
- Check Recommended Settings: If you are using a material listed in xTool Creative Space (XCS), select that material profile first. Use the recommended parameters provided by XCS.

- Manual adjustments (if no recommended parameters exist):
- If your material isn't listed, you may need to adjust manually. Scorching often means the laser is moving too slowly or dwelling too long. Try:
- Increasing speed.
- Decreasing power (if cutting through is not an issue, but scorching is).
- Reducing the number of passes (if multiple passes are used).
- Experiment methodically with small changes.
- Lower the focus: For cutting, you can lower the focus to get a better cutting performance.
- Try lowering the focus by 3mm and run a cutting test to see if the result improves.
- For more details on how to lower the focus, see this guide: https://support.xtool.com/article/1070.
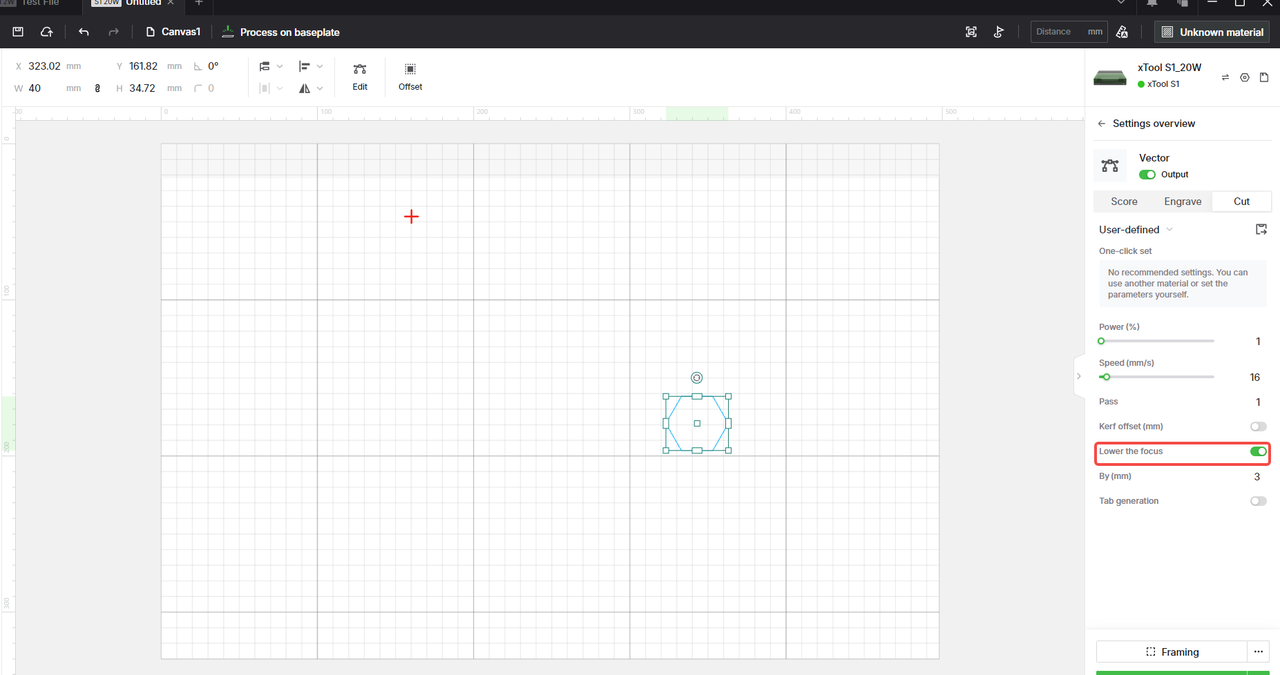
- Test on a Different Material: Try cutting a known, easy-to-process material like thin basswood plywood or cardboard using its recommended settings. If this cuts cleanly, the issue is likely related to the specific material you were initially using or its settings.
#2 Check focal distance (Auto-measure):
An incorrect distance between the laser module and the material surface means the laser is not focused correctly, leading to a wider beam, reduced cutting efficiency, and potential scorching.
- The "Distance" setting in XCS tells the machine the height of your material. Ensure this value is accurate.
- Perform Auto-measure: Click the "Auto-measure" button in XCS (as shown in the image below). Allow the machine to measure the distance automatically.
- Retry Cutting: After performing auto-measure, try the cutting process again.
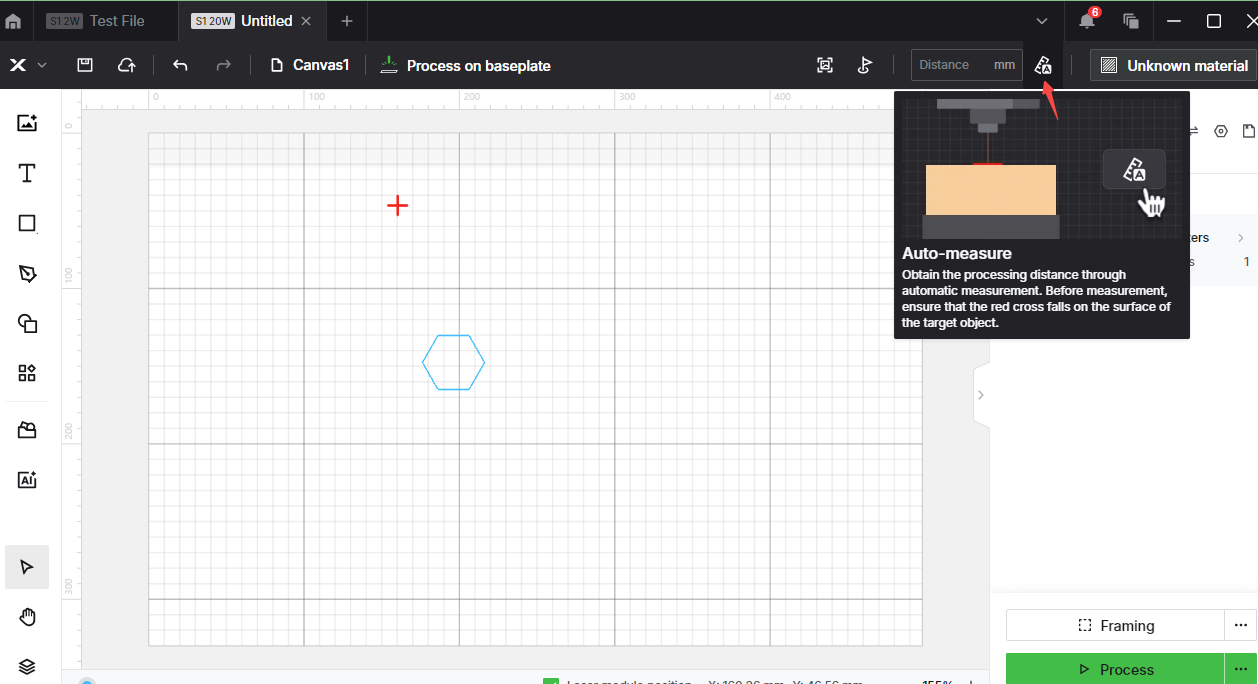
#3 Inspect laser lenses:
A dirty or damaged lens diffuses the laser beam, reducing power density and causing burning instead of clean cutting.
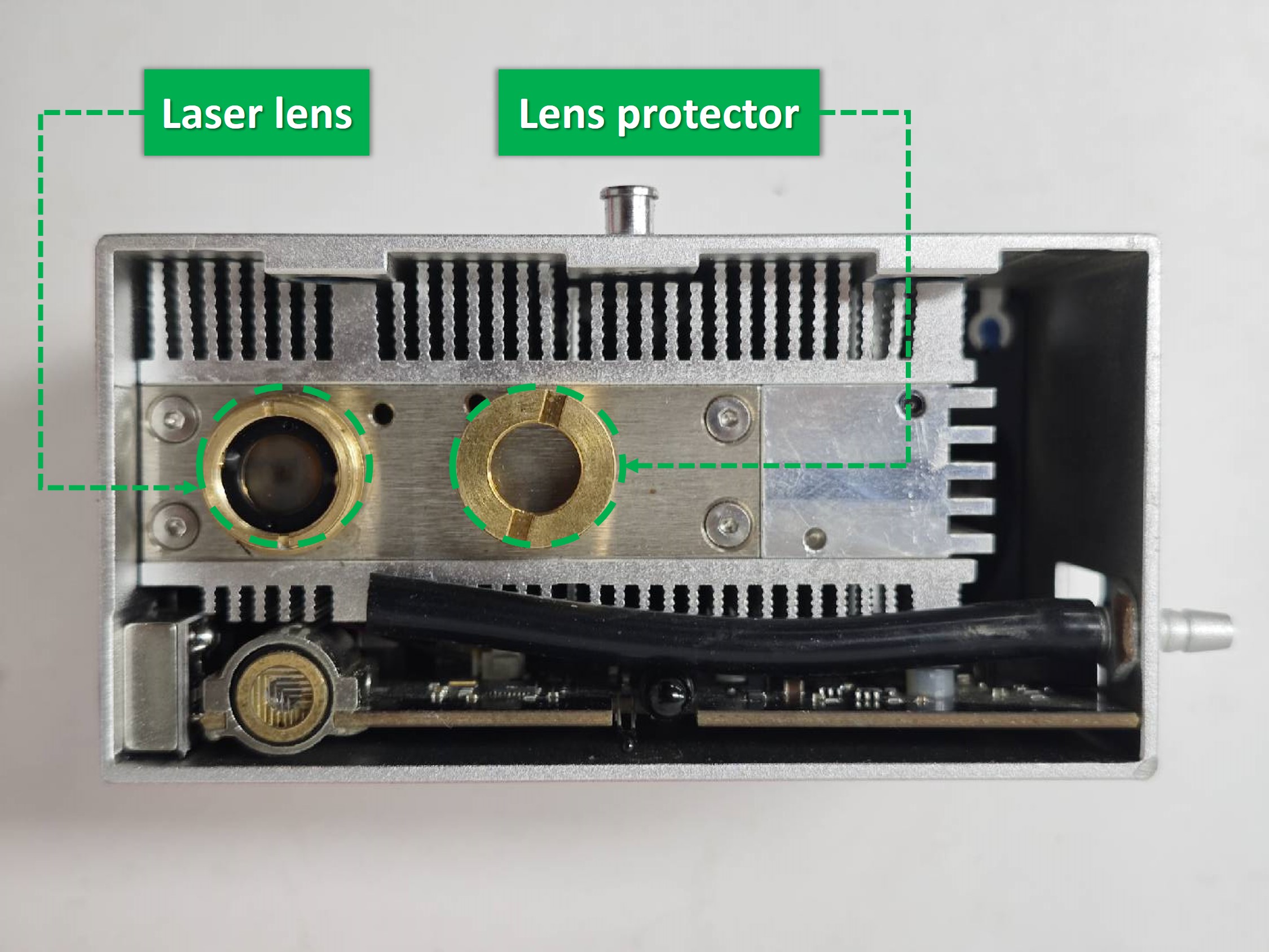
❗ Safety First: Ensure the machine is powered OFF and unplugged before inspecting or cleaning lenses.
- To inspect and clean the laser lens and its protector, please refer to this video guide: https://support.xtool.com/article/1066
- Clean if dirty: If the lens is dirty, clean it gently by following the cleaning procedure recommended by the video.
- Replace if damaged: If the laser lens or the protector shows signs of burns, cracks, or damage that cannot be cleaned, it must be replaced.
- For a replacement, please submit a ticket on https://support.xtool.com/submit-ticket. Please make sure to select “Buy after-sales materials” under the After-Sales Issues section. This will help our support team process your request more efficiently.
#4 Use Air Assist Set
Using Air Assist Set is very helpful to prevent yellowed/blackened edges.
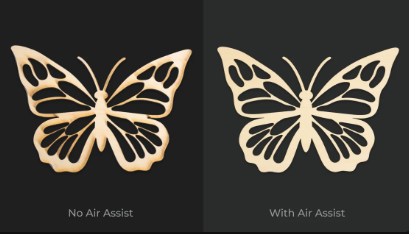
- Connect Air Assist Set to S1
- Set appropriate level:
- Click the gear button → Select Working info
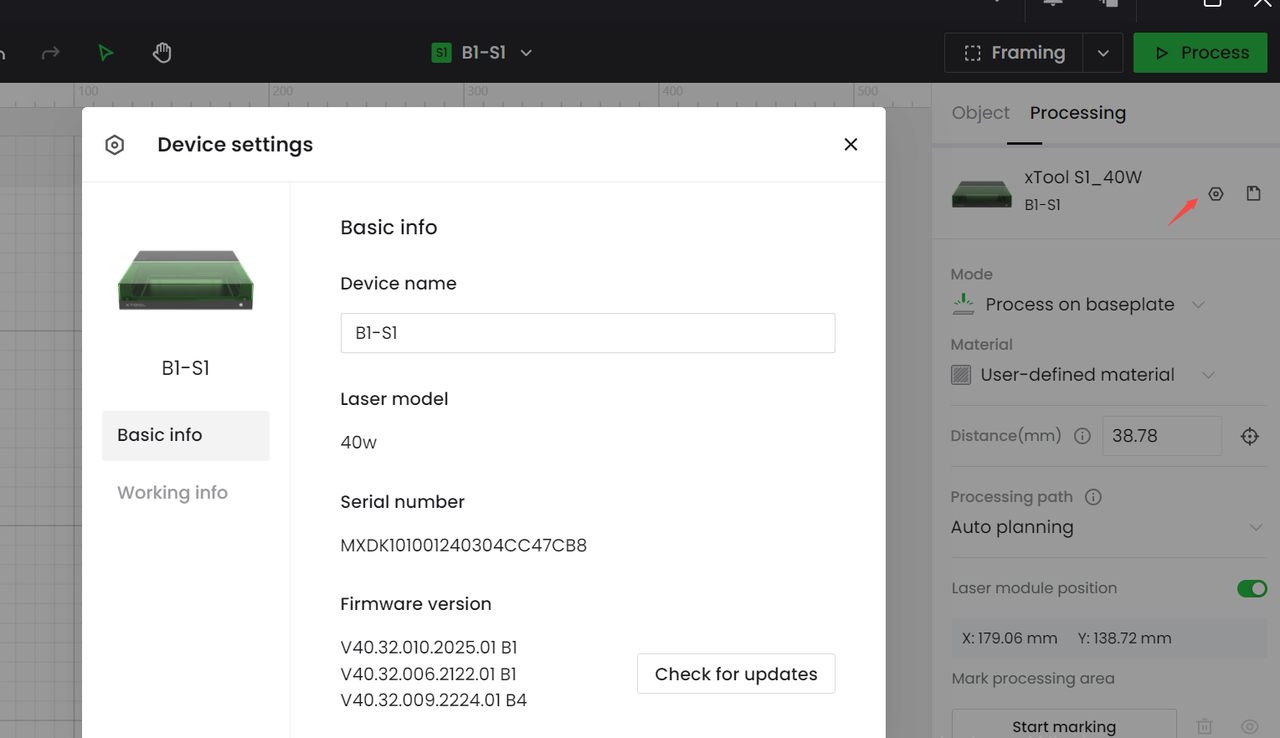
- For cutting, set the air assist level to Level 4. Try again and check the result.
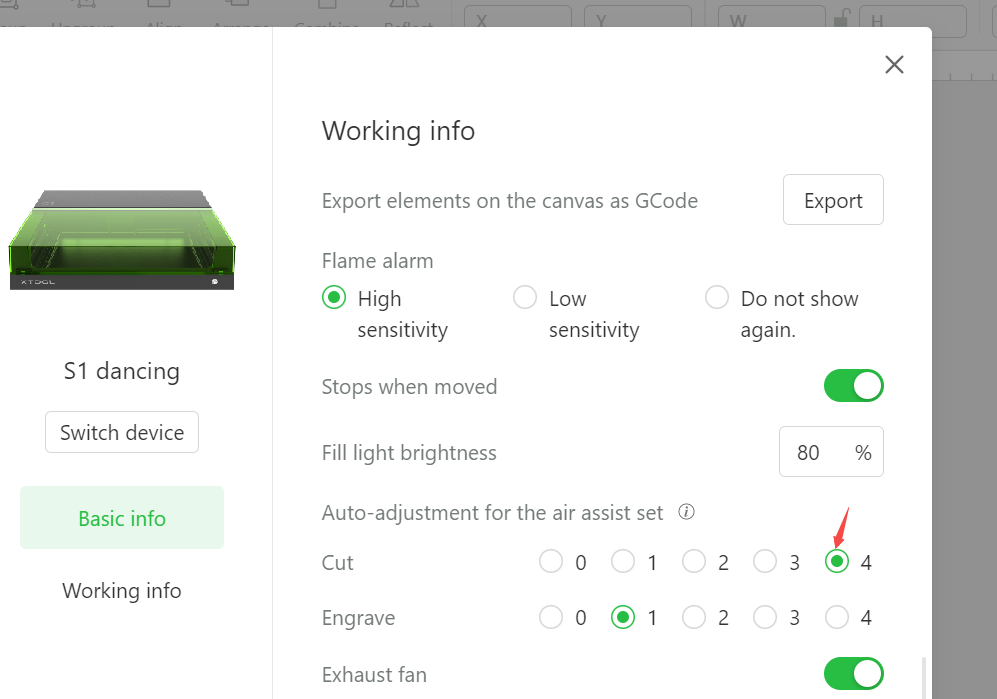
#5 Check Air Assist Set tube connection
Even if enabled in software, Air Assist Set won't function if the air tube is disconnected or loose.
- Inspect Connections: Check the air tube connection points:
- At the Air Assist Set outlet.
- At the air inlet port on S1.
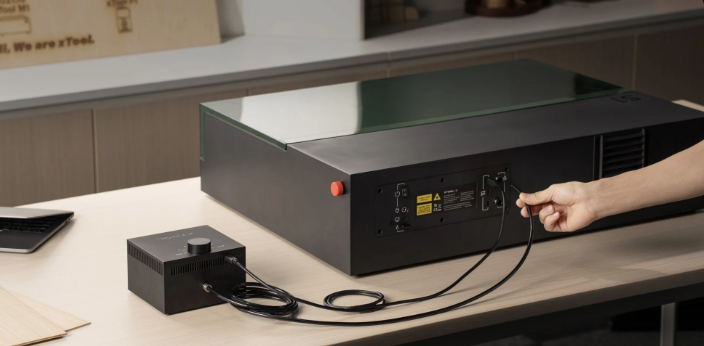
- Test airflow
- Turn the Air Assist Set on manually.
- Carefully place your hand near (but not touching) the laser nozzle outlet at the bottom of the laser module. You should feel a steady stream of air. Do not do this while the laser is active.
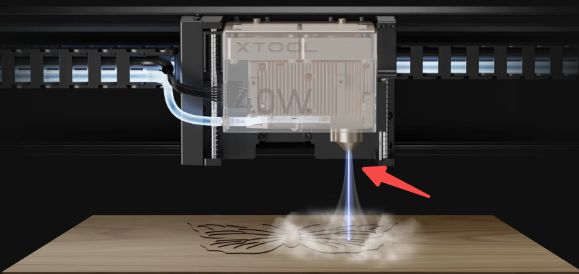
#6 Potential laser module malfunction
If you have meticulously checked all the above steps and are still experiencing significant yellowing/blackening on known compatible materials with appropriate settings, it might indicate an internal issue with the laser module itself.
In this case, please contact the xTool official customer service by submitting a ticket on https://support.xtool.com/submit-ticket.
- Please make sure to select “Buy after-sales materials” under the After-Sales Issues section and give a detailed description of the problem and the troubleshooting steps you have taken.
- If you're able to include photos or videos, even better — they can greatly help our support team understand the issue and process your request more efficiently.
Still experiencing issues?
Should the issue persist after completing the preceding steps, submit a ticket via the "Submit a Ticket" button in the "Help Ticket" section below. The standard response time for xTool Customer Service is one business day.
For a prompt resolution, please include the following details:
- Issue Description: A detailed explanation of the observed problem.
- Video Evidence: Attach a video demonstrating the issue, where applicable.
- Troubleshooting Performed: Any troubleshooting steps you have already attempted, along with their results.
This information is crucial for xTool technical support engineers to provide timely assistance.
Documentation feedback
Help improve this content by providing feedback. If this content did not meet your requirements, select "No" in the "Was this page helpful?" section below. Include specific details about what was unclear or missing in the pop-up suggestion box. Feedback submissions are reviewed by xTool technical writers to enhance future documentation.