1. The image is mirrored after engraving, why?
When setting parameters, you need to click the mirror input settings.
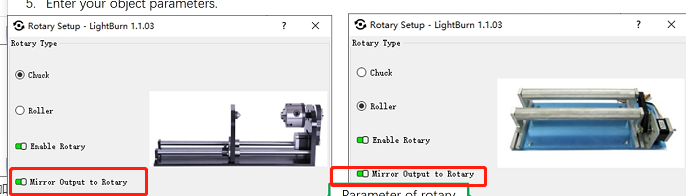
2. The rollers fail to grasp the material in cylindrical processing, why?
Rollers may fail to grasp the material in fast rotation due to the weak friction between rollers and the material. For vector paths, it is recommended that you choose jaw chuck components rather than rollers for cylindrical engraving.
For bitmap images, ensure that the material is properly placed on rollers. If so, ensure that the fixed roller is well connected with the shaft coupling during reinstalling the fixed roller.
3. How to engrave materials in larger diameters (>100mm) through the jaw chuck components?
We provide you with modifiable files of jaw chuck components, so you can change the lengths of the jaw components and make them by 3D printers to engrave materials in larger diameters.
4. Hard to install the tail module, why?
1. The screw to fix the tail module is tightened before installing the tail module.
2. The T sliding blocks of the tail module are not placed in the slots of the baseplate.
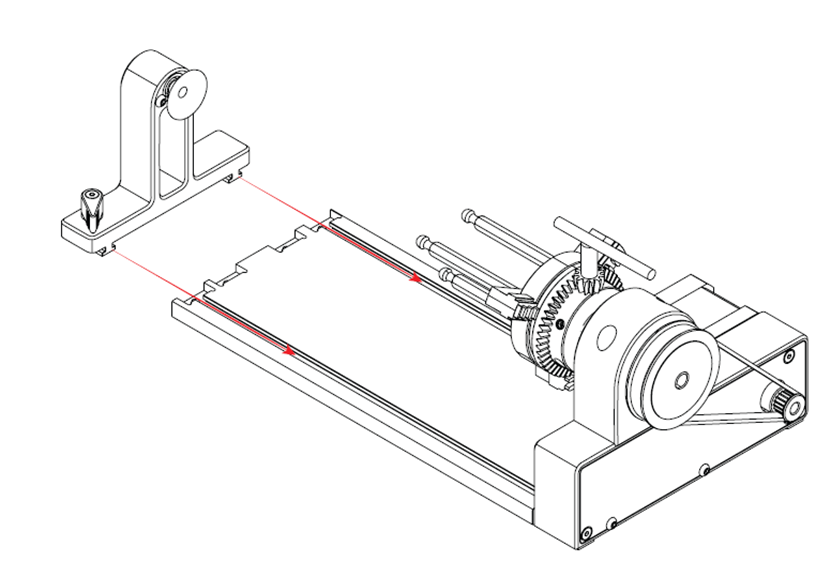
5. Is the rotary attachment compatible with a third-party laser machine?
The rotary attachment 2 is compatible with most frame structure laser machines, which include but are not limited to products from Atomstack, Ortur, Neje and Twotrees.
If you need to use a third-party machine, it's recommended to choose the rotary attachment 2 kit for D1, in which the adapter cable for a third-party laser machine is included.
Note: The rotary attachment 2 Pro kit for D1 on sale is compatible with some early third-party laser machines.
However, the new version of the rotary attachment 2 Pro kit for D1 later will not be compatible with any third-party laser machines.
6. How to connect the rotary attachment for xTool M1 to a third-party machine?
The rotary attachment 2 kit for M1 or rotary attachment 2 Pro kit for xTool M1 only includes one aviation cable. To connect the rotary attachment with a third-party laser machine, contact us at
support@xtool.com to purchase the adapter cable for a third-party laser machine.
Note: The rotary attachment 2 Pro kit for D1 on sale is compatible with some early third-party laser machines.
However, the new version of the rotary attachment 2 Pro kit for D1 later will not be compatible with any third-party laser machines.
7. Can I control the rotary attachment through Lightburn or LaserGRBL?
You can control the rotary attachment 2 through Lightburn or LaserGRBL as long as you can control your laser machine through it.
In Lightburn, you can set the parameters of the rotary attachment such as the diameter of the roller, the diameter of the jaw chuck, and the diameter of the material).
In LaserGRBL, set the Y-axis travel resolution (Y-axis travel resolution = 12800 / the perimeter of the material).
8. The material slides from grasp on rollers or on the jaw components, why?
Possible causes: the material is too heavy. (Maximum weight the rollers can support: 3 kg; maximum weight the jaw chuck components can support: 1 kg)
In cylindrical processing on rollers, ensure that the adjustable roller is properly connected with the driving belt as the following figure shows.
In cylindrical processing on the jaw chuck components, slow the processing speed and try again.
9. Distorted engraving with Lightburn, what should I do?
: Download and install
XCS software and update the firmware first if you were using Laserbox basic software when the problem occurred, then set the parameters in Lightburn (for D1) as shown below and try again:
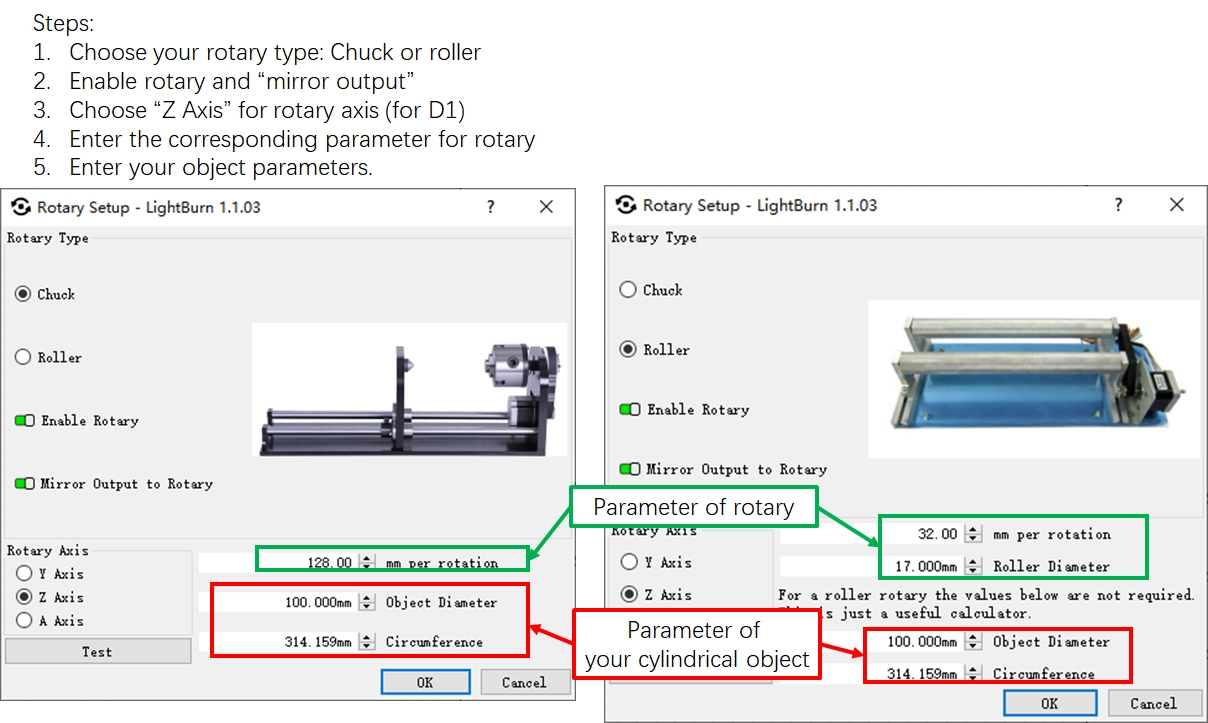
10. There are two types of connecting cables for the second-generation rotary accessories. What is the difference between the xTool D1 version and the xTool M1 version in appearance?
For xTool D1 & other open machines, Please use the flat connector wire (below).
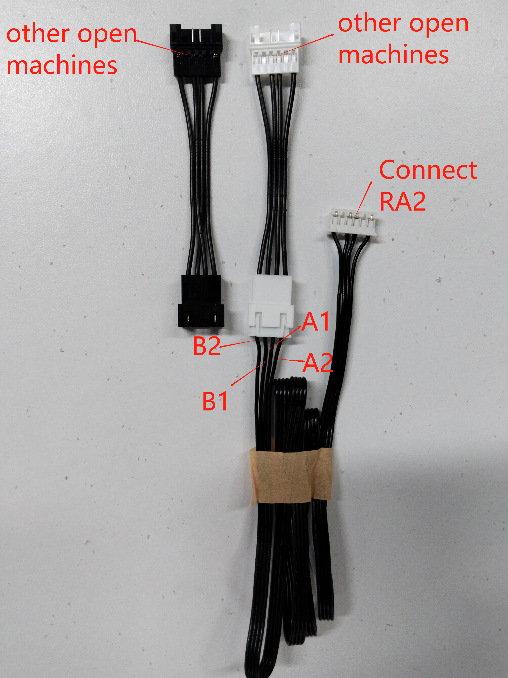
M1 machine, please use a circular connector (below).
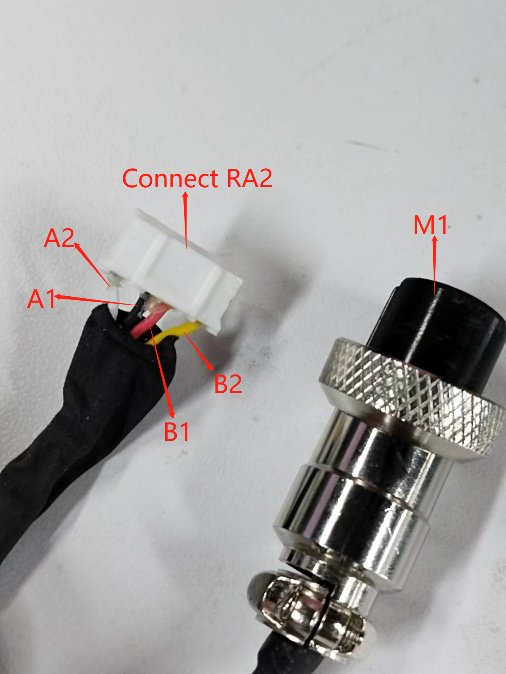
11. How much weight can the RA2/RA2 Pro support?
- Roller mode: Up to 3 kg
- Jaw mode: Up to 1 kg